Cryogenic Treatment

What is a cryo-processor?
It is a computer-controlled processor. It comes with proven processing cooling curves programmed into the computer. Any other desired cooling curves can be easily programmed into the processor. To run the Model 701 Cryo Processor, one icon is clicked and the program will run automatically.
It is a dry process. Liquid nitrogen is converted to a gas before it enters the chamber so that at no time does liquid nitrogen come in to contact with the parts assuring that the dangers of cracking from too rapid cooling are eliminated.
The model 701 uses conventional electrical cooling to reduce the temperature to -100°F, making it the most economical processor on the market. At -100°F, the liquid nitrogen system cuts in, and the dry vapors of liquid nitrogen are used to cool to the desired cycle.
The electric cooling has another advantage. At the end of the run the processor is set to hold a temperature below freezing and not return to room temperature where condensation and rusting can be a problem.
The standard Model 701 Processor uses 220 volt, single phase 11.2 amp service. For a small fee, any other power requirements can be built into the processor.
We list the capacity of the processor at 1500 lbs. We customarily run at 1800 to 2000 lbs. when we make our runs. We have run loads in excess of that although this practice is not recommended. When the processor is loaded about half full while running a normal load of ferrous tools, it uses about one pound of liquid nitrogen for every pound of material processed. Loads less then this are somewhat less efficient, while loads more the half are significantly more efficient.
Because of its ease of operation, its economy, and its great reliability, there are over 120 of these units running worldwide.
The question is often raised if the (heat) tempering should be performed inside the Cryo Processor or if it should be done in a separate tempering oven. We here at 300 Below Inc. considered that question very early in our existence. It certainly would make for a smoother running operation if the material did not have to be transferred from one vessel to another. We found that there are certain considerations that did not make tempering in the cryo processor a good idea:
First: different materials get different (heat) tempering cycles.
Second: different cross sectional areas need different tempering times. Therefore how would it ever be possible to run loads of mixed materials or sizes. If you do, it is a compromise at best.
Check out the Cryo-Processing Advantages Increases abrasive wear resistance
- 1. Requires only one permanent treatment
- 2. Creates a denser molecular structure. The result is a larger contact surface area that reduces friction, heat and wear
- 3. Changes the equipment's entire structure, not just the surface Subsequent refinishing operations or re-grinds do not affect permanent improvements.
- 4. Eliminates Thermal shock through a dry, computer controlled process.
- 5. Transforms almost all soft retained austenite to hard martensite.
- 6. Forms microfine carbide fillers to enhance large carbide structures
- 7. Increases durability or wear life.
- 8. Decreases residual stresses in tool steels
- 9. Decreases brittleness
- 10. Increases tensile strength, toughness and stability coupled with the release of internal stresses
Advantages of cryogenic treatment :
It has been observed that the process provides the materials a stronger, denser and more-coherent structure thus increasing the abrasive resistance and thermal and electrical conductivity. For steels, the explanation of the phenomena in Layman's terms is as follows: Super cooling the steel refines the carbides in the steel by expanding the carbide structure to fill any voids in the metal. Then as the higher temperatures return, everything relaxes into where it wants to be thus providing stability to the steel. Every step in the treatment is carefully controlled else the temperature extremes will shock the steel into delaminating.
Metallurgy of cryogenic processing :
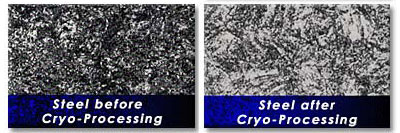
Two primary mechanisms are at work in cryo processing. Firstly, the super-cold treatment converts any retained austenite to marten site and the marten site is tempered as the metal return to room temperature. The martensitic structure resists the plastic deformation mush better than the austenitic structure, because the carbon atoms in the martensitic lattice "lock together" the iron atoms more effectively than in the more open-centered cubic austenite lattice. Tempering the martensite makes it tougher and better able to resist impact than un-tempered martensite. Secondly, cryogenic treatment of high alloy steels, such as tool steel, results in the formation of very small carbide particles dispersed in the martensite structure between the larger carbide particles present in the steel. This strengthening mechanism is analogous to the fact that the concrete made of cement and large rocks is not as strong as concrete made of cement, large rocks and very small rocks, (Coarse sand). The small & hard carbide particles within the martensitic matrix help support the matrix and resist penetration by foreign particles in abrasion wear.
Further explanation to the "Concrete effect" is as follows: Cryogenic treatment of alloy steels causes transformation of retained austenite to martensite. Freshly formed martensite changes its lattice parameters and the c/a ratio approaches that of the original martensite. Etta (h) carbide precipitate in the matrix of freshly formed martensite during the tempering process. This h carbide formation favours a more stable, harder, wear-resistant and tougher material. This strengthens the material without appreciably changing the hardness (macro hardness).
The other major reason for the improvement is stress relief. The densification process leads to an elimination of vacancies in the lattice structure by forcing the material to come to equilibrium at -1960C and lowering the entropy in the material. This lower entropy leads to the establishment of long range order in the material which leads to the minimization of galvanic couples in the material thus improving the corrosion resistance of materials including Stainless Steels.
Besides, there is some amount of grain size refinement and grain boundary realignment occurring in the material. These two aspects lead to a tremendous improvement in the electrical and thermal conductivity of the material thus transporting the heat generated during the operation of the tool away from the source and increasing its life.
Typical applications of the technology range from perishable tools and dies to alloy steel wear parts, gun barrels, machine knives and blades transmission gears, shafts, bearing cams, automobile engine parts, camera parts and microelectronic circuits, guitar strings and other musical horns, copper electrodes and the list goes on. This treatment can be carried out on tools and components which have been provided various coatings to enhance certain material characteristics and the net result is an increase in the performance of the coating over and above the existing coating. This has been found useful in the case of TiN, TiCN, Ti Al N, Hard Chrome, Stellite etc. coatings on various materials to enhance their wear resistance.